Overview
The following tutorial is designed to help users of SafeGrid Earthing Software to learn about and practice the application of powerful operating tools and principles.
Mobile phone repeater station earthing arrangement
The mobile phone repeater station earthing consists of interconnected grid conductors covering the lease area of 9 m by 14.5 m of conductors buried at a depth of 0.5 m. The grid is buried at separation distances of 0.5 m and 1 m from the perimeter fence and the shelter building respectively.
There are three 1 m2 buried plates underneath the concrete pad footing for each leg of the antenna structure.
Rods of 12 m lengths are added as required to reduce the overall earthing resistance.
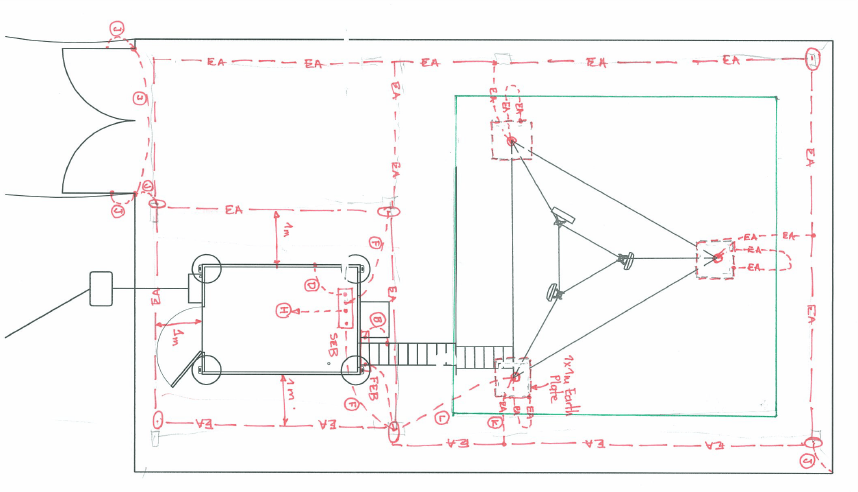
Purpose of the earthing system
Modelling the earth grid in SafeGrid
The model includes the metal plates which were modelled as tightly meshed straight line connected segments.
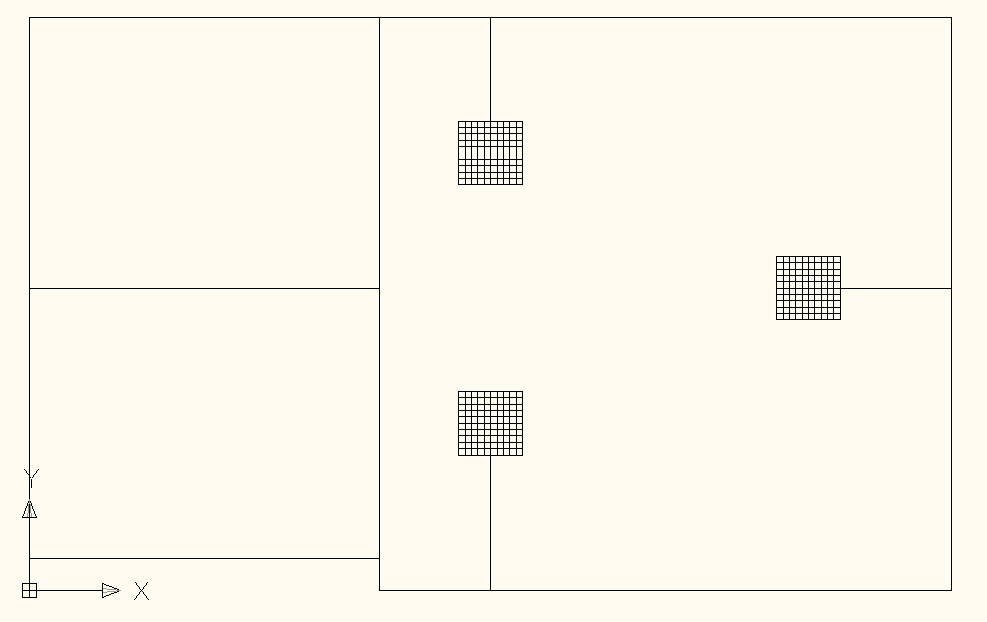
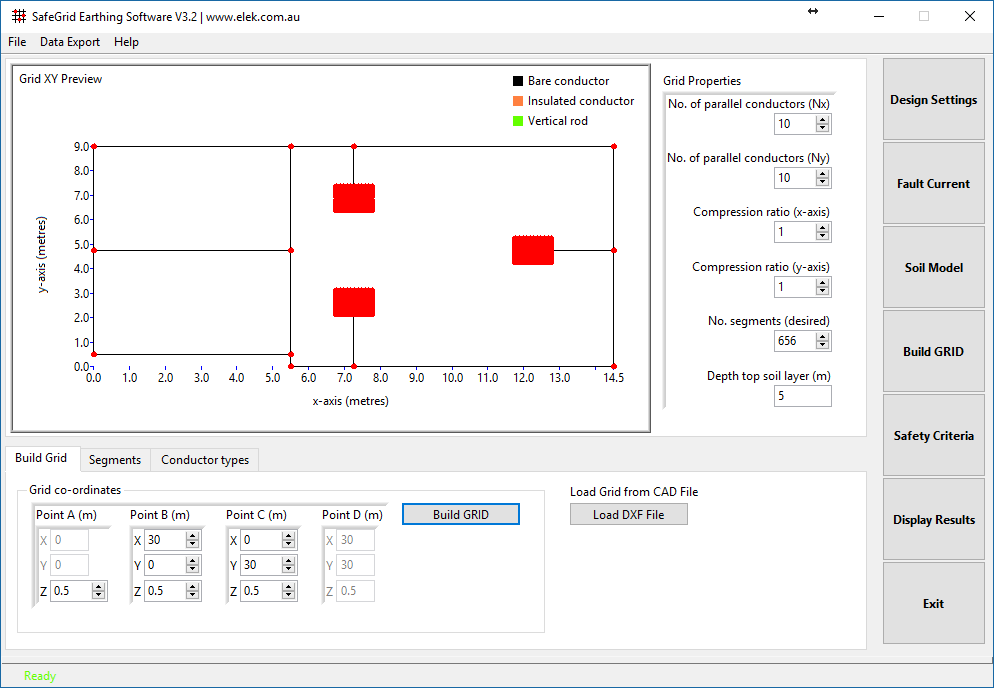
Soil resistivity modelling
Soil resistivity measurements were taken in the field using the Wenner Array Method at electrode spacing’s of between 1 m and 8 m due to space limitations.
Two sets of measurements were taken in different directions. Note it is good practice to take at least 5 measurements per set.

Depth of top layer = 3.13 m
Bottom layer resistivity = 139.3 Ω-m
Goodness of fit = 0.928 (very good)
SafeGrid Results – calculated grid resistance
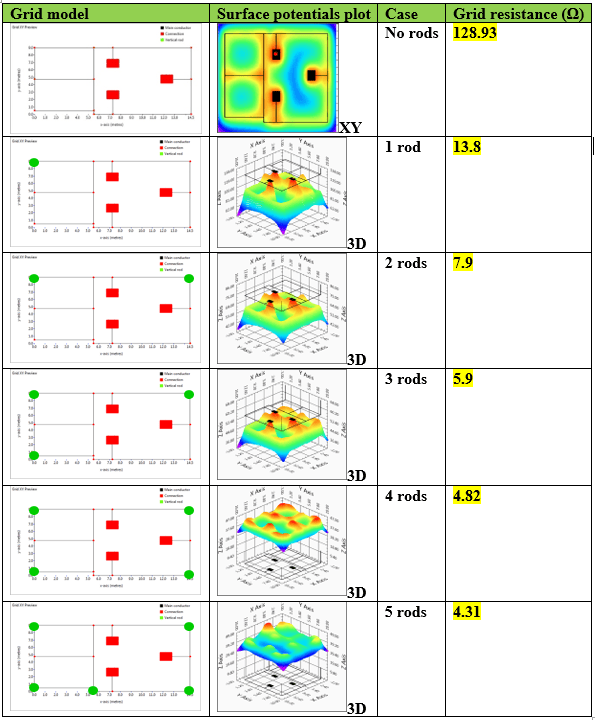
Plot of grid resistance versus no. of rods
