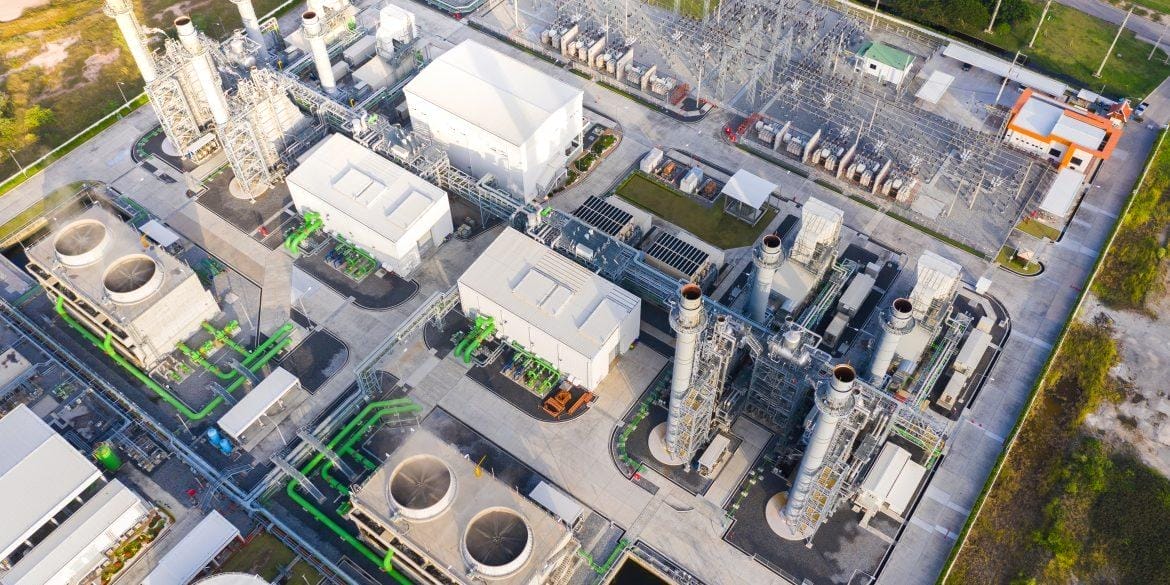
Table of Contents
Earthing Systems Explained
An earthing system (IEC) or grounding system (IEEE) connects an electrical power system with the earth’s surface, for both safety and functional purposes. Earthing systems also affect electromagnetic compatibility and are required for lightning protection systems.
Earthing systems fall under two categories: system grounding and equipment grounding.
System grounding is the deliberate connection to earth of a phase or neutral conductor to control voltage stress and voltage hazards (touch or step voltages) to within safe limits.
Equipment grounding is to electrically interconnect or to ‘bond’ the non-current carrying conductive parts of equipment together and to the earth.
Earthing systems must be carefully designed. There are many earthing and grounding system related standards the designer needs to consider.
Low voltage earthing systems
IEC terminology
IEC terminology from the IEC 60364-1 standard [2].
First Letter – Relationship of the power system to the earth:
- T = direct connection of one point to earth.
- I = all live parts isolated from earth, or one point connected to earth via a high impedance.
Second letter – Relationship of the exposed-conductive-parts (ECPs) of the installation to earth:
- T = direct electrical connection of ECPs to earth, independently of the earthing of any point of the power system.
- N = direct electrical connection of the ECPs to the earthed point of the power system (in AC systems, the earthed point of the power system is normally the neutral point or, if a neutral point is not available, a line conductor).
Subsequent letter(s) (if any) – Arrangement of neutral and protective earthing conductors:
- S = protective earthing function provided by a conductor separate from the neutral conductor or from the earthed line (or, in AC systems, earthed phase) conductor.
- C = neutral and protective earthing function encapsulated into a single conductor (the PEN conductor).
TN Systems
TN, or Terre-Neutral, systems are electrical systems where the Exposed Conductive Parts (ECPs) are directly connected to a solidly grounded point of the source [1]. TN systems have low fault loop impedances but carry a higher risk of damage to the neutral (with even a risk of fire) due to higher fault currents. Additionally, earth electrodes need to be installed at regular intervals (connected to each conductor in the system) to avoid safety issues.
TN Systems can be sorted into multiple different types, depending on the arrangements of the conductors.
TN-S
The TN-S is the first type of TN configuration. This configuration of system is typically used in industrial and commercial applications, where two different wires act as a protective conductor and a neutral conductor [1]. TN-S systems tend to be the safest option of the TN varieties due to the separation of the protective earthing and the neutral and can even be used with flexible conductors or smaller conduits.
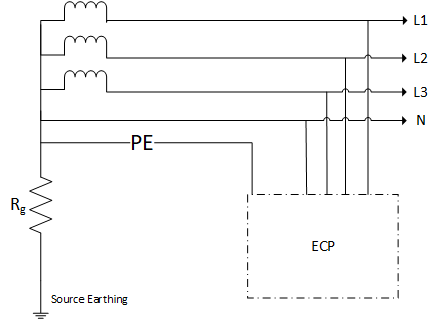
As can be seen in Figure 1 above, the TN-S system has the neutral and the protective earth (PE) connecting ground, from the same point, to the ECP using different conductors. TN-S systems can also be used in instances where there is no neutral (such as with a three-phase supply in a delta configuration), so long as there is a PE conductor present.
TN-C
The TN-C system is the second type of TN configuration. Unlike the TN-S configuration, the TN-C configuration combines the protective earthing and neutral into a single conductor. This is a configuration typical of utilities in North America, but not a recommended practice for industrial and commercial power systems [1]. One of the benefits of using a TN-C system is reduced cost, due to the elimination of a device pole and a conductor, but this compromise results in reduced safety (such as increased risk of fires or disruption by electromagnetic interference).
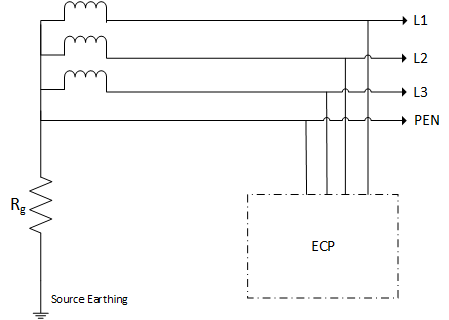
As can be seen in Figure 2 above, the TN-C system differs from the TN-S system by combining the PE and neutral functions into a single conductor, the Protective Earth Neutral (PEN) conductor.
TN-C-S
The last type of TN system is the TN-C-S system. In North America, the transition point from PEN to PE is typical of the utility to user interface with inclusion of an electrode for an intentional connection to earth at the service entrance [1]. TN-C-S systems combine the benefits of the TN-C system with the TN-S system, but with reduced returns (i.e., TN-C-S systems are not as safe as TN-S system and not as cheap as TN-C systems).
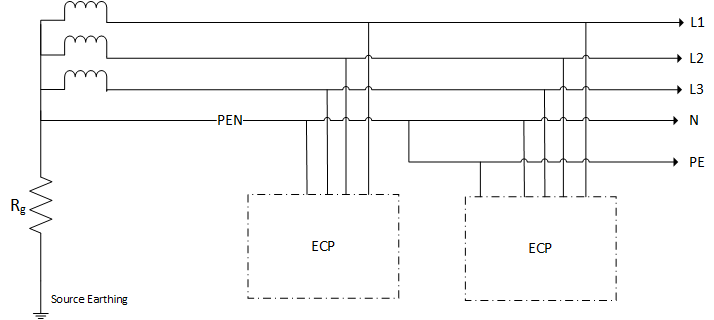
Figure 3: Diagram of a TN-C-S system
As can be seen in Figure 3 above, the TN-C-S system combines the function of both the TN-C and TN-S systems, where certain ECPs will be connected to ground via the PEN conductor, and others will be connected to a PE and neutral conductor, both of which are split from the initial PEN conductor.
TT System
TT, or Terre-Terre, systems are electrical systems where the loads being supplied are connected to ground electrodes that are independent of ground electrodes connected to the source [1]. TT systems tend to not require continuous monitoring (with the exception of any RCDs, or residual current devices, connected to the ECPs). One deficit of the TT system is the high loop impedance, which causes high step voltages and leakage currents, meaning RCDs are required for the usage of this system.
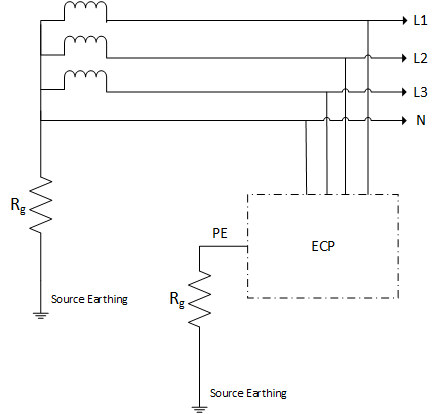
Figure 4: Diagram of a TT system
From Figure 4 above, it can be seen that the system grounding occurs at two different points: The first being the point where the neutral conductor is connected, and the second being the point where the PE conductor is connected. These two grounding points are independent of each other.
IT System
IT, or isolation terre, systems are electrical systems where the source is insulated from the ground or connected to it with incredibly high impedance. To prevent potential damage from fault currents, IT systems are able to be earthed both individually and collectively [1]. IT systems offer the best continuity of service during operation (i.e., insulation faults are very easily caught and eliminated without much disruption), but also requires a high degree of maintenance. Additionally, the earth fault loop impedance is very high due to the high level of insulation in the network, and IT systems run the risk of having two simultaneous fault currents in the network.
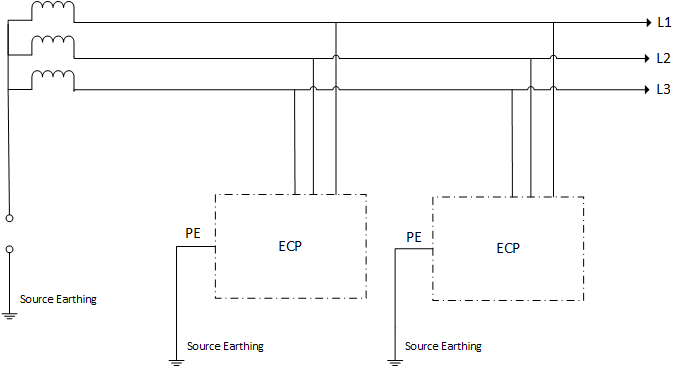
Figure 5: Diagram of an IT system with individually earthed ECPs
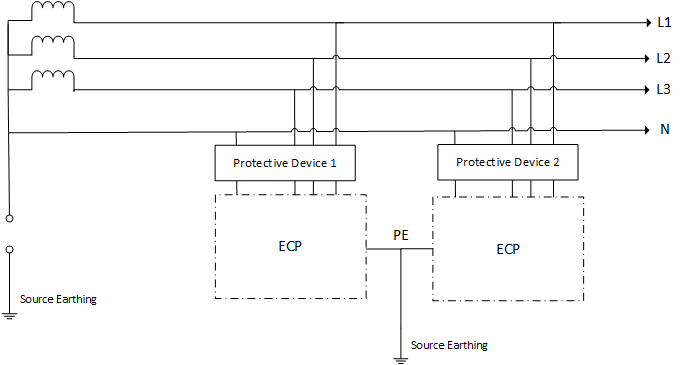
Figure 6: Diagram of an IT system with collectively earthed ECPs
Both Figure 5 and Figure 6 show examples of an IT system. Note that in both examples, the system is grounded through an incredibly high impedance (i.e., the open circuit), and the PE conductor is grounded separately. Figure 5 shows an instance where the ECPs have independent PE conductors, whereas Figure 6 shows an instance where the ECPs have a common PE conductor.
DC Systems
DC, or direct current, systems are a type of system earthing designed for direct current rather than AC, or alternating current. They are usually earthed via a positive and negative pole using a two-wire system [2]. The aforementioned systems have a DC system equivalent that differs from their AC counterparts functionally.
Comparison of Low Voltage Earthing Types
The advantages and disadvantages of the low voltage earthing methods are summarised below:
High voltage earthing systems
High voltage (above 1 kV) earthing systems have three fundamental requirements:
- Safety of people.
The earthing system shall not impose any person including those in the public population any unreasonable risk.
The main hazard to a person associated with earthing systems is current flowing through the heart leading to ventricular fibrillation.
- Protection of equipment.
The earthing system should provide for the expected operation without damage to any equipment. Specifically, this means the earthing system must be capable of (a) withstanding fault currents; (b) maintaining integrity for the lifetime of the installation; (c) avoiding damage to equipment due to excessive voltage rise or current flows during faults; and (d) contributing to ensure system electromagnetic compatibility.
- Operational security.
The earthing system must support operational security by maintaining a dependable voltage reference.
Solid grounding
Solid grounding refers to connecting a system supply, such as a generator neutral or a transformer, directly to the ground without any intervening impedances. This is a particularly good way to avoid excessive fault currents. The effectiveness of a solidly grounded system can be determined by comparing the ground-fault current to the three-phase fault current. The higher the ground-fault current compared to the three-phase fault current, the greater the degree of grounding in the system.
Ungrounded
In an ungrounded system, there is no direct connection whatsoever between the system supply and the ground. They are only connected to each other via capacitive coupling [1].
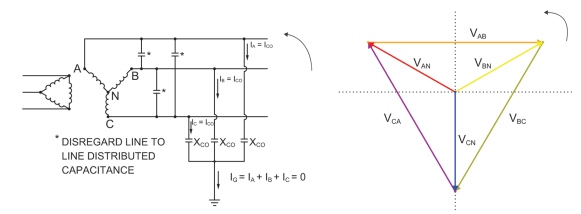
Figure 7: A circuit diagram and phasor diagram for an ungrounded system
Figure 7 shows a circuit diagram and a phasor diagram for an ungrounded system. Not that the system is grounded via 3 parallel capacitors, labelled XCO. These represent the capacitive coupling via which the system is grounded. Both the neutral and the protective earthing are grounded via this capacitance.
Resistance grounded
A resistance grounded system will have the system supply connected to the ground via a resistor. Limiting current via a resistor has several benefits, including reduction of burning and melting effects in faulted equipment, reduction of mechanical stresses in circuits, and reduction of electric-shock hazards to personnel, to name a few.
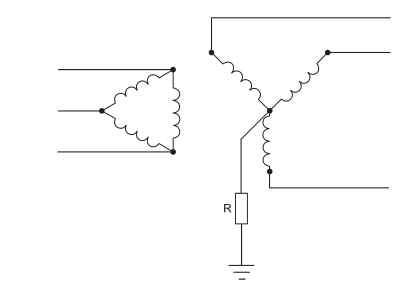
Resistance grounded systems can be low-resistance or high-resistance, depending on the desired outcome. Low-resistance grounded systems can be beneficial for limiting the ground-fault current between 50 A and 1000A, whereas high-resistance grounded systems are good where the ground-fault current is less than 10 A in magnitude.
Reactance grounded
Resonant grounding and ground-fault neutralisers
Resonant grounding is the connection of a reactor between supply system neutral and ground to eliminate reactance in a system via resonance. Ground-fault neutralisers are the reactors that are connected between a system supply neutral and the ground. For the resonant grounding, the reactor is specially selected or tuned to resonate with the distributed capacitance of the system, so that the ground-fault current becomes mostly resistive with a low magnitude.
A reactance grounded system will have the system supply neutral connected to the ground via a reactor (capacitor, inductor, choke, etc). Reactance grounding is typically used when there is a desire to limit the ground fault magnitude to a value much like the magnitude of a three-phase fault.
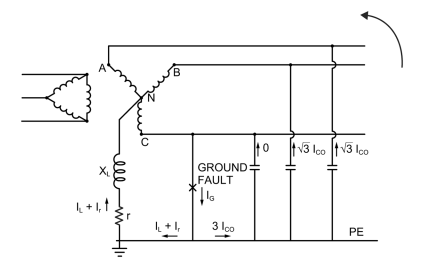
Figure 9: Diagram of a resonance grounded system using ground-fault neutralisers
Figure 9 shows an example of a resonance grounded system, with the usage of a ground-fault neutraliser. Note that the introduction of the inductor, XL, is used to counter the effects of the capacitive coupling to the ground, thus making the ground fault current almost purely resistive.
Comparison of High Voltage Earthing System Types
The advantages and disadvantages of the high voltage earthing methods are summarised below:
Parameter | Ungrounded | Solid | Reactance Grounding | Ground-Fault Neutraliser | Resistance Grounding | ||
---|---|---|---|---|---|---|---|
Low value reactor | High value reactor | Low Resistance | High Resistance | ||||
Current for phase-to-ground fault in percent of three-phase current | Less than 1% | Varies, may be 100% or greater | Usually designed to produce 25% to 100% | 5% to 25% | Nearly zero fault current | 20% and downward to 100 A and 1000 A | Less than 1% but not less than system charging element, 3ICO |
Transient | Very high | Not excessive | Not excessive | Not excessive | Not excessive | Not excessive | Not excessive |
Line-to-neutral loads | Not supported | Supported | Supported if current 60% or greater | Not supported | Not supported | Not supported | Not supported |
Surge arresters | Ungrounded-neutral type | Ungrounded-neutral type | |||||
Remarks | Not recommended due to overvoltages and nonsegregation of fault | Generally used on systems (1) 600 V and below and (2) over 15 kV | Not used due to excessive overvoltages | Best suited for application in most medium voltage industrial and commercial systems that are isolated from their electric utility system by transformers | Generally used on systems of 2.4 kV to 15 kV, particularly where large rotating machines are connected | Used on systems up to 5 kV |
Risk-based approach
Generally, it is incredibly difficult to eliminate all hazards associated with earthing systems. Risk management typically involves the minimisation of hazards to an acceptable statistical degree rather than eliminating them. Relatively new Standards such as AS 2067 [3] provide methodologies for risk-based calculations for earthing systems design.
Touch and step voltage hazards and the risk-based approach
The most significant threat facing a person involving earthing systems is the risk of ventricular fibrillation due to current flow in the heart. This depends on a person’s physiology, duration of current flow, amount of current and whether the current will interfere with the persons heart cycle. Details about the probabilities related to the effects of current on the human heart and heart/body impedance can be found in IEC 60479 [4].
Achieving negligible hazard levels is rarely possible. Determination of the hazard level is related to the risk of fibrillation and the usage of probability calculations as detailed in IEC 60479.
If hazards cannot be reduced, risk assessment must be employed. This should include the occurrence rate and duration of faults, along with the frequency and duration of contact for a person on-site. Risk mitigation should be applied as reasonably practicable, where the cost is not grossly disproportionate to the benefit gained.
References:
[1] IEEE Std 3003.1-2019 Recommended Practice for System Grounding of Industrial and Commercial Power Systems.
[2] IEC Std 60364-1 Low Voltage Electrical Installations – Part 1: Fundamental principles, assessment of general characteristics, definitions.
[3] AS 2067:2016 Substations and high voltage installations exceeding 1 kV a.c.
[4] IEC 60479-1:2018 Effects of current on human beings and livestock – Part 1: General aspects.