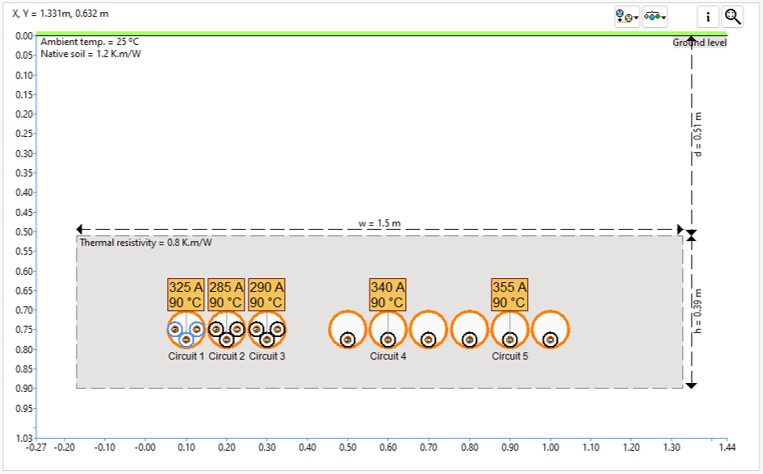
Table of Contents
Why is backfill used for buried cables?
Soil backfill refers to the material used to fill trenches after laying buried cables. This backfill material ensures the cable installation’s ampacity, reliability, and longevity. The key functions of soil backfill are adequate thermal heat dissipation, mechanical protection, and stability during external pressures.
Native soil is a common backfill material, involving reusing the excavated or displaced soil. It is the only option for installing offshore cables using cable ploughing equipment. Where local regulations allow it, native soils for backfill of land-based cables are installed at local moisture and compaction levels that provide maximum thermal dissipation and prevent movement or settlement.
Alternatives to native soil backfills include engineered backfills such as stabilised sand, sand-cement mixes (typically 14:1), and fluidised backfills that mix sand, cement, water, agents, and other components.
It’s worth noting that fluidised backfills are increasingly preferred in modern installations due to their ease of application and reduced risk of cable damage. Unlike traditional backfills that require compaction, fluidised backfills flow around cables, minimising the potential for mechanical stress or damage during installation.
Although the cost of a properly engineered and installed backfill is greater than using native soil, the major benefits include an increase (often significant) in cable current rating due to its low thermal resistivity, reduced electrical losses and cost savings over the lifetime of the cable system, and protection against moisture migration (soil drying) due to its good thermal stability.
Thermal resistivity of native soils
The soil’s thermal resistivity is very sensitive to soil moisture content, which depends on rainfall and moisture migration (soil drying) caused by cable heating.
Soil comprises solid soil grain particles, air voids, and water. Table 1 gives the typical thermal resistivity of different materials. Soil grains have a thermal resistivity of 0.11 to 1.7 K.m/W. The thermal resistivity of still water is 1.65 K.m/W, and that of air is approximately 40 K.m/W.
Table 1 – Thermal resistivity of materials [ref. 1]
Material | Thermal resistivity (K.m/W) |
---|---|
Quartz, average | 0.11 |
Granite | 0.25-0.58 |
Limestone | 0.45 |
Sandstone | 0.58 |
Mica | 1.7 |
Water | 1.65 |
Organic material | 4 (wet) to 7 (dry) |
Air | 40 |
Table 2 gives the thermal resistivity of soils in situ based on soil moisture and weather (rain) conditions. Deciding on the thermal resistivity of soil to use for cable rating studies is challenging. One has the option of using standardised values, such as from IEC 60287-3-1, but these do not account for the local soil conditions, leading to a significant risk that over the life of the cable, it may be subject to overheating.
Table 2 – Thermal resistivity of soil [ref. 2]
Thermal resistivity K.m/W |
Soil conditions | Weather conditions |
---|---|---|
0.7 | Very moist | Continuously moist |
1.0 | Moist | Regular rainfall |
2.0 | Dry | Seldom rains |
3.0 | Very dry | Little or no rain |
Thermal resistivity of concrete
Concrete is commonly used as a thermal backfill material for underground high voltage power cables due to its beneficial thermal properties. Unlike soil, concrete does not experience moisture migration or drying out, maintaining stable thermal performance over time.
The thermal resistivity of concrete used for cable backfill typically ranges from 0.5 to 1.0 K.m/W. Some specific values include:
- Standard concrete: 0.6-1.0 K.m/W
- Dense concrete: 0.5-0.7 K.m/W
- Lightweight concrete: 1.0-1.5 K.m/W
Some manufacturers offer specialised thermal concrete products for cable backfill with even lower resistivity:
- Thermocrete: A cement-bound sand product with thermal resistivity as low as 0.33 K.m/W.
- Powercrete: A high-performance heat-conducting concrete with very low thermal resistance.
The low and stable thermal resistivity of concrete makes it an excellent backfill choice for high voltage underground cables, allowing for higher current ratings and more reliable long-term performance compared to native soil backfills.
Thermal resistivity of engineered backfills
To improve the thermal performance of the cables and mechanical strength of the trench an engineered backfill material is used and envelopes the cables. A good engineered backfill consists of a finely graded material (specified based on sieve analysis) that are well-compacted and should have a wet thermal resistivity of 0.35 to 0.45 K.m/W and a dry thermal resistivity of 0.9 to 1.1 K.m/W.
For a given backfill, the dry density has the highest impact on thermal resistivity under completely dry conditions. The thermal resistivity of a backfill depends on moisture content. The properties of materials used for backfill is provided in table 3 below.
Table 3 – Thermal resistivity of soil and backfill materials [ref. 3]
Types of Soil or Backfill | Saturated (Wet) Moisture Content (%) | Dry Density (kg/m3) |
Thermal Resistivity (K.m/W) Wet |
Thermal Resistivity (K.m/W) Dry |
---|---|---|---|---|
Fine-coarse gravel | 3-5 | 2150 | 0.5 | 2.5 |
Gravelly sand | 7-15 | 2050 | 0.5 | 2 |
Fine-coarse sand | 12-18 | 1900 | 0.5 | 1.7 |
Uniform sand | 12-18 | 1700 | 0.55 | 3.5 |
Sandy silt | 15-25 | 1800 | 0.65 | 2.5 |
Silt | 15-25 | 1750 | 0.7 | 2.5 |
Silt clay | 20-30 | 1750 | 0.65 | 2 |
Lean clay | 20-30 | 1700 | 0.75 | 2.5 |
Fat clay | 30-40 | 1600 | 0.9 | 3.0 |
Stone-dust | 9-12 | 2050 | 0.45 | 1.1 |
It is common for an engineered backfill to be provided with a thermal dry-out curve. A typical curve is shown below and shows that as the moisture content reduces the thermal resistivity increases.
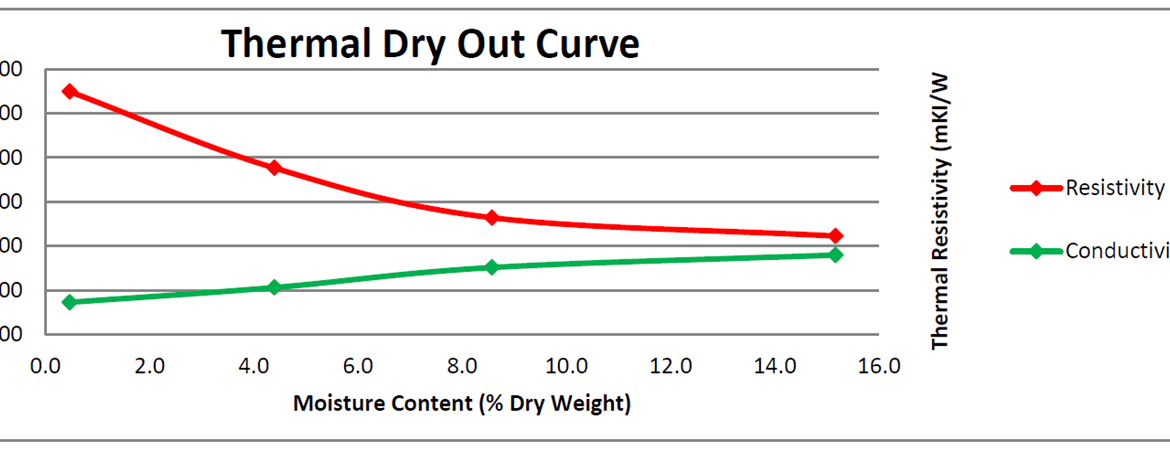
Figure 1 – Example thermal dry-out curve of an engineered backfill material
The thermal resistivity of a backfill depends on its compaction level, which affects the water content. A high level of backfill compaction provides good thermal performance. A backfill cannot be devoid of water content; it must be made wet during installation and compaction around the cables and must not be dry.
There is an optimum water content that will have a maximum density. A moisture-to-density curve for a particular backfill material (obtained using the Proctor test in a laboratory) determines the density at the optimum moisture content. According to [ref. 3], the optimum moisture for granular, non-cohesive soils (like sand) is about 8 to 12 %, and the soil appears quite wet.
The maximum density in the curve below is 2120 kg/m3 at a moisture content of 7.6 %.
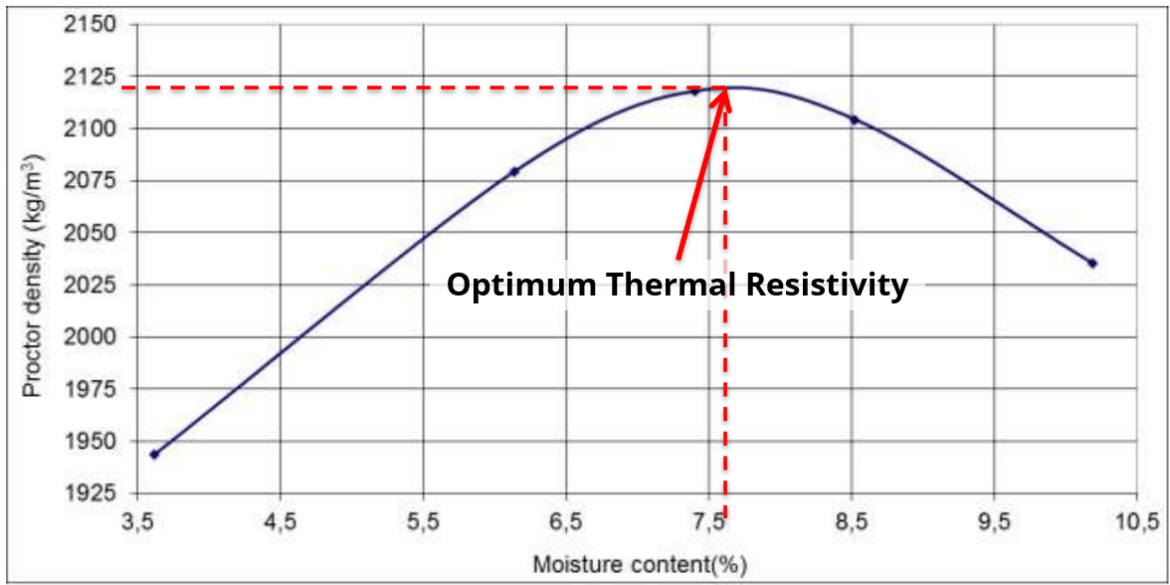
Conclusions
It’s difficult to decide on the thermal resistivity of soil or backfill to use for cable rating studies. For decades, engineers have struggled with this problem.
Field instrumentational monitoring can provide useful information (relatively cheaply) by obtaining actual soil thermal resistivity and rainfall data over time.
Field samples of native soils and engineered backfills should be obtained and laboratory-tested for cable systems design.
The impacts of soil drying (dry-out) on the cable current rating should be considered. Where a conductor’s maximum permissible operating temperature is above 70 degrees Celsius, the thermal resistivity of the backfill encapsulating the conductors, if it is within a 50 degrees Celsius isotherm, then its thermal resistivity should be based on 0 % moisture content (completely dry).
Backfills must be fit-for-purpose and properly installed, meaning properly (but carefully) compacted.
The operating temperature can be monitored using distributed temperature sensors (DTS) to avoid overheating of installed cables.
References:
[1] AIEE Committee. (1960). Soil Thermal Characteristics in Relation to Underground Power Cables. AIEE Committee Report.
[2] International Electrotechnical Commission. (2017). IEC 60287-3-1:2017 – Electric cables – Calculation of the current rating – Part 3-1: Operating conditions – Site reference conditions. Geneva, Switzerland: IEC.
[3] CIGRÉ. (2018). Technical Brochure 714 – Guide for Thermal Rating Calculations of Cables. Paris, France: CIGRÉ.