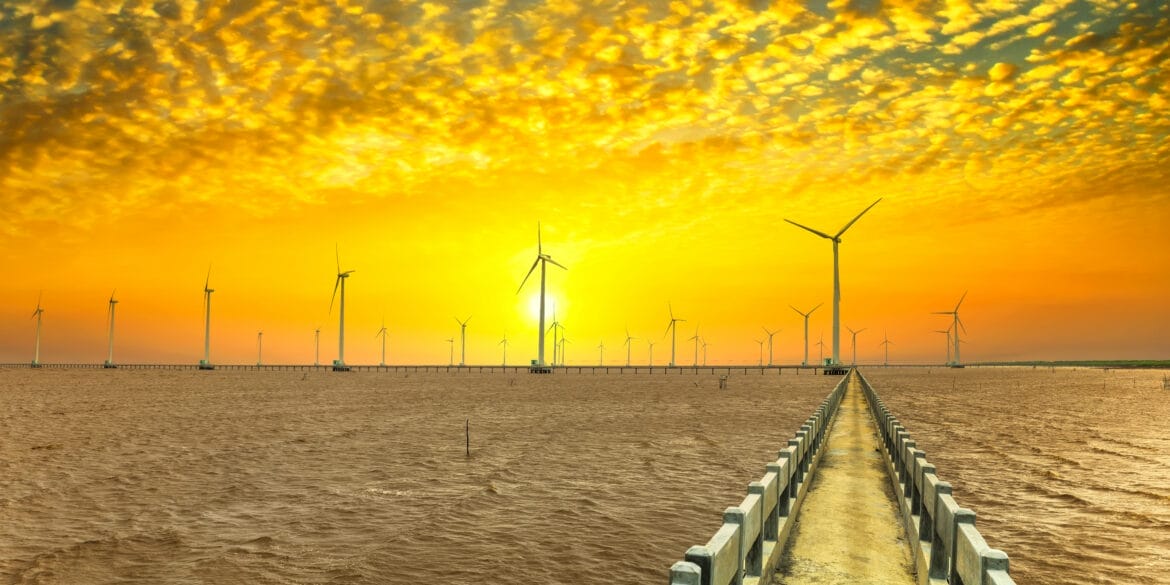
Several factors must be considered when selecting cable tray materials for offshore installations such as wind turbines or oil rigs, including corrosion resistance, fire safety, and economic aspects.
The harsh marine environment presents unique challenges that require careful material selection to ensure longevity and performance.
The following advice is based on extensive field experience [ref. 1].
Recommended Materials for Offshore Applications
For offshore facilities, the following materials are commonly recommended for cable trays:
Stainless Steel 316L
Offers excellent corrosion and fire resistance.
It is a universal solution but expensive and heavy.
Glass Reinforced Polyester (GRP)
Excellent corrosion resistance.
Limited by requirements for sun resistance and electrostatic accumulation.
It is not recommended for telecommunications cables due to the lack of electromagnetic protection.
Aluminum Alloys (5XXX and 6XXX series)
-
Best quality/price ratio.
-
Approximately half the price and weight of stainless steel.
-
30% less in price and weight than GRP.
Best Practices for Aluminum Alloy Cable Trays in Offshore Environments
By adhering with the following best practices, aluminum alloy cable trays can offer significant weight and cost savings (up to 50% compared to stainless steel and 30% compared to GRP) while maintaining durability and safety in offshore environments.
Parameter | Recommendations |
---|---|
Material Selection | Use copper-free aluminium alloys from the 5XXX or 6XXX series, such as 5754 or 6063. |
Magnesium Content |
Limit magnesium content to 4% (by weight) to reduce thermite sparking hazard.
Thermite sparking is a potential fire and explosion hazard that can occur when aluminum comes into contact with rusty steel under certain conditions. |
Installation Zones for Hazardous Areas | Aluminum alloy cable trays may be installed in Zone 1 and Zone 2 areas, provided the risk of impact is low. Installation zones refer to specific areas classified according to their potential for explosive atmospheres. |
Corrosion Prevention | Use isolation materials (e.g., nylon washers, EPDM rubber bands) between aluminum trays and steel supports. Employ bimetallic Cu/Al washers for grounding connections to prevent galvanic corrosion. Ground cable tray systems approximately every 30 meters. |
Fire Safety | Adhere to regulations and procedures to minimize thermite sparking risk. |
Maintenance | Properly installed aluminum cable tray systems require minimal maintenance. |
References:
[1] Desmoulière, L. (n.d.). CABLE TRAYS OFFSHORE: A CHOICE OF MATERIALS. CTS CES, Issy-les-Moulineaux, France, 2009.
[2] NEMA VE 1-2017, “Metal Cable Tray Systems,” National Electrical Manufacturers Association, Rosslyn, VA, 2017.
[3] NEMA FG 1-2018, “Nonmetallic Cable Tray Systems,” National Electrical Manufacturers Association, Rosslyn, VA, 2018.