Click through the steps in the window below. Turn on your speakers to hear the voiceover.
ELEK SafeGrid Earthing Software can simulate an earthing or grounding system impedance test performed using the fall-of-potential (FOP) method.
The grid under study and the remote electrode are modelled, and a unity current is simulated as flowing between them. Ground surface voltage is measured along a line in the simulation, just like in the test. The complete step-by-step procedure is explained in the section below.
Fall-of-potential method explained
With the FOP method, the resistance of an earthing system is measured using a remote earth electrode. The remote electrode should ideally be located at an infinite distance from the earthing system where the earth’s current density approaches zero. In reality, the remote electrode is located at a distance of at least five (5) times the maximum diameter of the measured earthing system (IEEE Std 81).
A current source is connected to the grid being measured to measure grid resistance, and the remote earth electrode causes a current to flow through the soil. A voltage measurement circuit is then connected to the main earthing system, and a sensitive voltage measurement device is used to measure the ground surface voltage at points equidistance apart along a line starting from the main earthing system toward the remote electrode. The measured surface voltages are converted into apparent impedance as follows:
Apparent resistance = (grid injection point voltage – surface point voltage) / injected current.
Apparent impedance is plotted versus the distance from the grid being measured. The shape of the apparent impedance curve between the grid being measured and the remote electrode should rise steeply, flatten out (rise slowly) towards the middle, representing a zone where the interaction of the tested and return electrodes is small, and rise again steeply approaching the remote electrode.
There is a theoretical position of 61.8 % of the separation distance between the measured grid and the remote electrode, which is the correct position for measuring the exact grid impedance for uniform soil resistivity.
The FOP measurement method is very useful. It is widely used and has several variations. Refer to the article Testing of Earthing Systems for detailed information and the testing procedure.
Fall-of-potential method limitations
Limitations of the FOP method include:
- An accurate measurement of apparent impedance is possible only when the grid’s current density fields produce a hemisphere with an electrical centre. It may be very difficult to obtain a result for grids that are either large or complex in shape or with interconnected earth return paths.
- The 61.8 % rule does not apply for non-homogeneous (multilayered) soils, and the apparent resistance curve’s flat portion may lie between 10 % and 90 % along the distance.
- In non-homogeneous soils, the appropriate probe position cannot be determined by simple observation of the shape of the apparent resistance curve. Rather, a computer simulation of the grounding system and test circuit must be performed to predict the appropriate voltage probe position (IEEE Std 80).
Steps to FOP test modelling in SafeGrid
- Model your primary grid conductor system in Build Grid. In this case, the grid is 60 by 30 metres with 28 off vertical rods. The soil model is three-layer with top layer 100 Ohm.m of 1 m thickness, middle layer 200 Ohm.m of 1 m thickness, and bottom layer 300 Ohm.m of infinite thickness,
- Add a remote current injection segment (vertical rod) in Build Grid at a distance at least five times greater than the maximum diagonal of the primary grid. In this case, the diagonal distance of the grid is approximately 67 m; therefore, the remote current injection segment is located at x = 390 metres.
To add a rod go to Drawing Tools >> Add Rod then enter the rod length, and X- and Y-coordinates. - Create multiple faults in Design Settings. The first fault is 1 A (1+0i), and the second is -1 A (-1+0i). Frequency = 1 Hz.
- Apply the 1 A (1+0i) fault to the primary grid injection segment (Segment 36) and the -1 A (-1+0i) fault to the remote current injection segment (Segment 75) in Build Grid.
- Create a Line voltage profile in Safety Criteria starting at the primary grid injection point and up to 95 % of the distance to the remote current injection segment. In this case, the line voltage profile is set with Point A at x=30 m, y=15 m, and Point B at x’=372 m, y’=15 m.
- Press Calculate in Display Results. Note the calculated grid impedance is 2.522 Ohms. Generate a custom report including the Segment voltages table. From the custom report, obtain the segment voltage of the primary grid injection segment. In this case, the voltage of segment 36 is 2.39 V (2.39+0i).
- Go to Safety Criteria and open the Touch voltages From the Reference dropdown, select Constant voltage and enter the segment voltage of the primary grid injection segment (obtained from the custom report in the previous step). In this case, the voltage is 2.39 V (2.39+0i).
- Go back to Display Results and press Calculate again, then open the Touch Plot. Note that the touch voltage plot is a plot of apparent impedance.
Conclusions
According to the Fall of Potential rule, the calculated grid impedance is expected to be at a distance of 61.8 % from the current injection point. In our case 222 m is 61.8 % away from the injection point. Zooming into the touch plot at 222 m, we can see that the apparent impedance at that point is 2.5 ohm which corresponds to the apparent grid impedance calculated in SafeGrid.
Closer examination of the difference between the theoretical 61.8 % and the accurately calculated SafeGrid impedance value reveals a small error of 0.41 %.
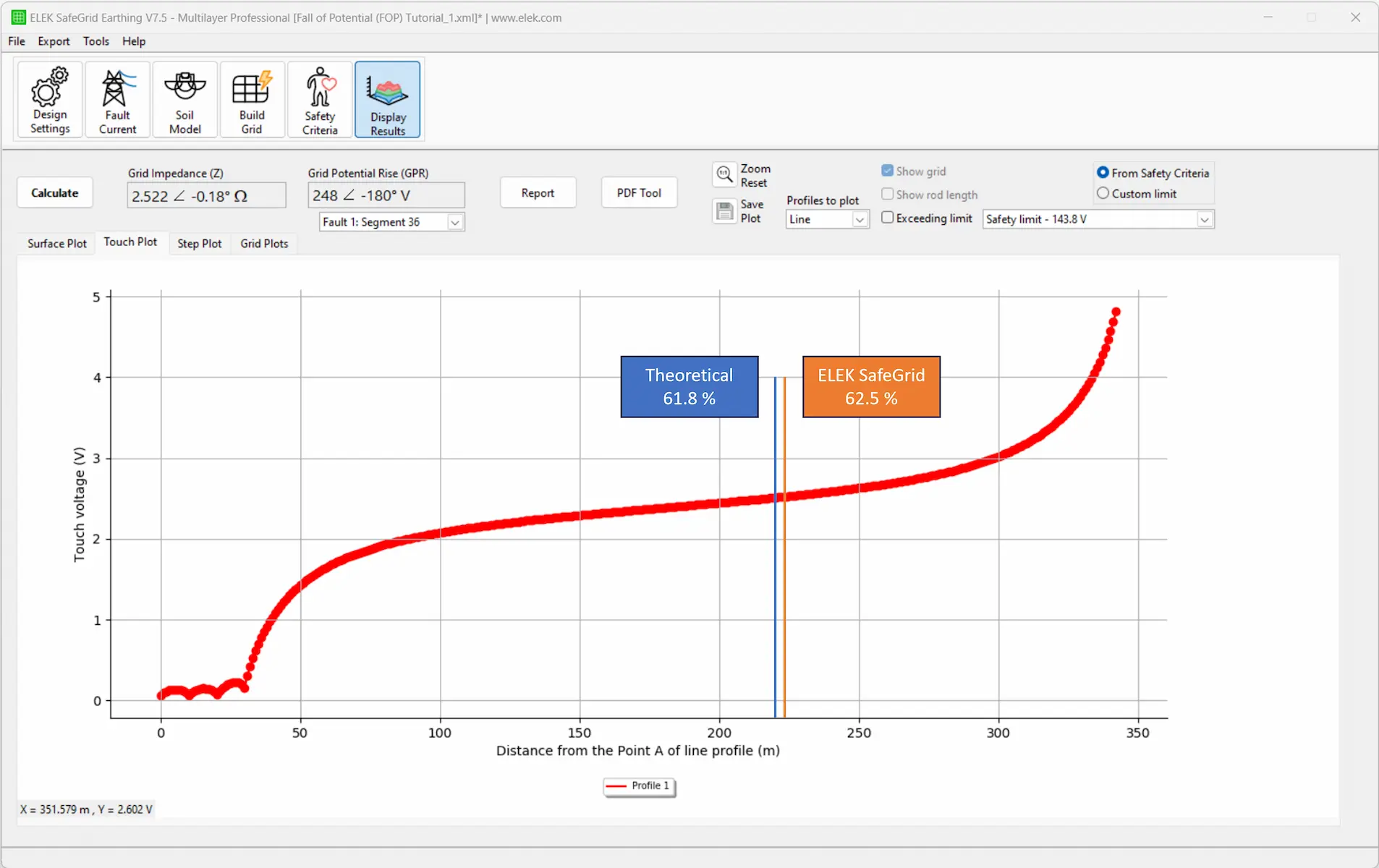
In many other cases the 61.8 % rule may be inaccurate and should be used with caution. The comparison below was for the same grid but with a different soil model. The soil model was low resistivity 50 Ohm.m over 2000 Ohm.m, resulting in a much larger error difference.
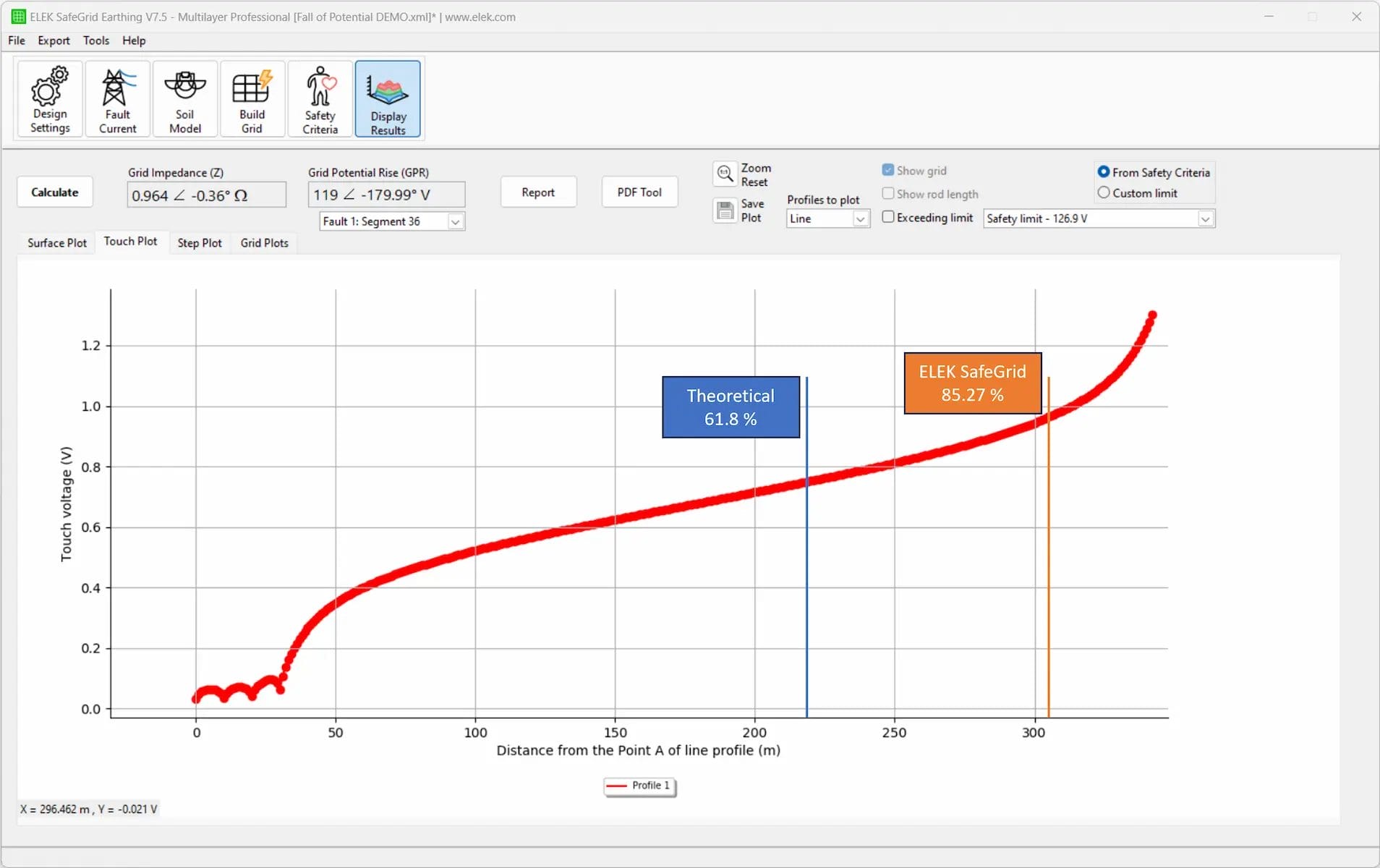